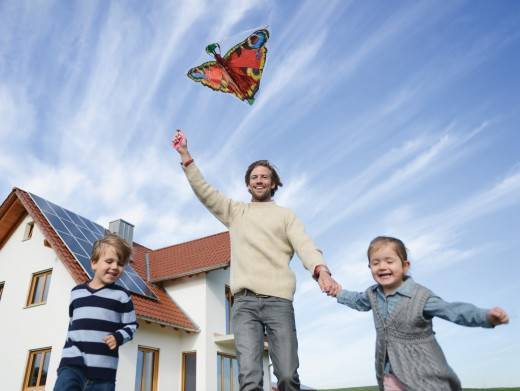
Ventilation at its most basic level can be as simple as opening a window to let the stale air out and the fresh air back in; however, the opportunities for opening windows in the UK are limited by weather conditions, heat loss and security. Up until quite recently, dwellings were designed to include only the most basic ventilation products, ranging from air bricks to window trickle vents and more latterly, simple extract systems. Unfortunately for just as long, properties have also suffered from the effects of condensation caused by inadequate means of ventilation.
Recent developments in the design and build of domestic properties have led towards ever more energy efficient homes, which aim for superior thermal performance and far greater levels of air tightness to minimise heat loss; thereby causing a subsequent increase in the use of balanced mechanical ventilation technologies. This adoption has also been reinforced by changes to Building Regulations Parts F and L, which are driving the need for good quality and sustainable ventilation solutions more than ever before.
These ventilation systems and component parts must also be highly energy efficient if they are to play a part in reducing a property’s overall carbon footprint and ongoing energy usage. Clearly, opening a window or relying on an air brick is no longer an option, but then neither is using cheap and by its nature, low quality mechanical ventilation appliances. So how do you ensure the equipment you specify/install provides a genuinely sustainable ventilation system that meets Building Regulations and NHBC guidelines, is SAP listed and enables you to comply with the Code for Sustainable Homes?
You may think I am going to start with mechanical ventilation, but it’s ducting that’s my first port of call and that’s for good reason; no matter how sophisticated the chosen mechanical system is, if poor quality ducting is used, the benefits from the system are significantly reduced.
Specify substandard ducting and it could mean anything between the ventilation system not meeting Building Regulation requirements to a room with an ugly stain in need of redecoration as a result of condensate leakage.
The ducting must have exacting tolerances, i.e. a good fit of rigid extruded systems, such as Domus rigid duct. If the duct bows, or looks concave, or the wall thickness appears uneven, the tolerances will be too wide. If the duct doesn’t retain its shape, it can be difficult to fit together and result in air or condensate loss. Always opt for a duct system which has all the accessories you need to create the ventilation system as a whole and that has been designed to work in harmony as part of a system and finally, third party tested for end-to-end system performance.
Alternatively, you might want to consider semi-rigid duct systems, such as the Domus Radial duct system, as an alternative to traditional ducting, especially for whole-house ventilation where space can be an issue. Traditional duct systems are based upon a branch design, with duct to rooms running off a main trunk connected to a Mechanical Extract Ventilation (MEV) or Mechanical Ventilation with Heat Recovery (MVHR) unit. A Radial system works differently in that each room vent is served by twin or single Ø75mm semi-rigid duct which connects to a distribution manifold, therefore providing a more even air flow. The manifold(s) is then connected to the mechanical appliance. For MEV and MVHR applications, the system benefits from less air leakage and improved air flow and a greater degree of room to room acoustic separation.
It is vital to insulate ducting in colder areas such as loft spaces, to remove the possibility of condensation forming and to maintain thermal efficiency. As recommended by the NHBC, insulating duct in warm spaces with a solution which needs to include an integral vapour barrier in certain applications is also equally important, Unfortunately some existing duct insulating products are unable to meet current Building Regulations which specify a minimum standard equivalent to a material of ≤0.04W/(m.K) at 25mm thickness. In order to do so it’s essential to use an insulation system such as patent accepted Domus Thermal, which is an engineered interlocking EPS (expanded polystyrene) system which exceeds the equivalent requirement at just 20mm thickness. The chosen insulation system must fit snugly around the duct and fittings with no air gaps and should be easy to install and secure once on.
The latest NHBC guidelines reinforce current Building Regulation requirements for not only ducting passing through cold spaces but also for insulating ducting between an MVHR appliance and the external terminals even when installed within the heated/insulated areas of the property; to avoid condensate forming on the outside of these colder ducts.
Which now brings me on nicely to Mechanical Ventilation with Heat Recovery (MVHR) systems.; MVHR systems work on the principle of extracting and re-using waste heat, such as that found in a bathroom or kitchen. MVHR systems efficiently pre-warm and filter fresh air drawn into the building with waste stale air using a heat exchanger; more than 95% of waste heat can be recovered by this mechanism. The filtered, pre-warmed air is then distributed around the home.
According to the Zero Carbon Hub, in 2012 more than 24,000 MVHR units were installed in the UK and it seems that this is an increasing trend that will continue. There are many MVHR systems available today, but as with most things they vary in quality and effectiveness. The good news is that the best performing models are easy to identify by their heat exchange performance and Specific Fan Power, which are listed on the Product Characteristics Database (PCDB). Polypipe’s Silavent Green Line HRX2 currently tops the list with a heat exchange efficiency of up to 95%.
Other key considerations when selecting an MVHR unit for maximum sustainability are the incorporation of a summer bypass facility which helps prevent homes from overheating during the warmer months and the type of fan built into the system. To comply with Building Regulations, specifying an MVHR or MEV unit with a low Specific Fan Power (SFP) – no higher than 1.5 Watts per litre per second (W/l/s) for MVHR or 0.7 W/(l/s) for MEV, is very important. A low SFP results in minimal energy usage and maximised air flow performance.
Bathroom and kitchen fans also play a key role in most aspects of domestic ventilation, be they axial, centrifugal, wall or window mountable, or in-line versions. The SFP requirement for fans is set by Building Regulations but there are other considerations to take into account when looking for energy savings. One of these, and often overlooked, is the fan’s energy consumption when in standby mode.
Domestic fans containing electronic controls, such as an overrun timer, can use anywhere between an extra 10-20% of the overall power used, when in standby. This actually means that despite a very low SFP, some fans will actually use more energy in standby mode over time. For example, a 6 Watt low energy fan running for a total of one hour per day consumes about 2kWh per year; astonishingly, on standby for the remainder of the day it uses a further 10kWh; therefore increasing the fan’s carbon consumption. Our own Silavent Green Line range of 100mm axial fans have been designed to use up to 70% less power when in standby mode than other low energy fans which, when combined with an SFP of 0.22 W/(l/s), makes them the most energy efficient range of axial fans available.
But it’s not just equipment that makes a ventilation system sustainable. If you have gone to the trouble of identifying the most energy efficient and highest quality ventilation equipment, you must also ensure it is correctly installed.
Well engineered and designed ventilation duct systems maximise airflow, reduce air leakage and achieve greater system performance – vital in whole house ventilation systems. However, poor quality ventilation installations are in abundance; with grilles missing, duct sections not being sealed at joints, inappropriate use of low cost flexible duct, where rigid ducting should be used; and too many sharp bends in the duct system leading to reduced air flow. Due to such widespread poor installation practice which affects system efficiency – most notably the SFP – heavy penalties are applied to SAP calculations, the official method used to calculate the energy consumption in dwellings.
Changes to Building Regulations Part F, Ventilation, directly addressed this by requiring a ‘qualified’ installer to commission new ventilation systems and submit a commissioning report to the Building Control Body (BCB). The Department of Energy & Climate Change (DECC) has also now stated that it will reduce SAP penalties if the systems are installed by a member of a registered Competent Person Scheme. The installation must meet the performance laid out in the original system design and an inspection checklist must be completed and submitted to Building Control. A check box in the SAP 2009 programme needs to be completed to enable improvement to the overall energy rating.
However, existing training schemes have made limited progress according to the Zero Carbon Trust Ventilation and Indoor Air Quality (VIAQ) Task Group and members are calling on the Department of Communities and Local Government to consider mandatory competency requirements for MVHR installations so that standards can be improved.
Working closely with the VIAQ Task Group, the NHBC has introduced a new chapter in their 2014 specification document, dedicated entirely to MVHR and is ikely to be taken very seriously by developers and builders alike.
With all new homes expecting to reach zero carbon from 2016, which requires six points under the Code for Sustainable Homes and most new homes coming in at just three points, developers and builders have a considerable task ahead of them. MVHR and MEV systems are playing a role in this and are becoming ever more popular as a relatively low cost way of moving towards the zero carbon goal. But simply fitting any MVHR or MEV system isn’t good enough and fitting one poorly is no better. Take the time to research the most energy efficient, well designed and well made ventilation system and ensure it is designed, installed and commissioned competently, for a highly sustainable, long lasting, energy efficient ventilation solution.
Polypipe Ventilation provides customers with a complete sustainable ventilation package, with ducting and appliance working in harmony, to meet the most demanding of energy efficiency targets. For more information please email vent.marketing@polypipe.com or call 03443 715523.